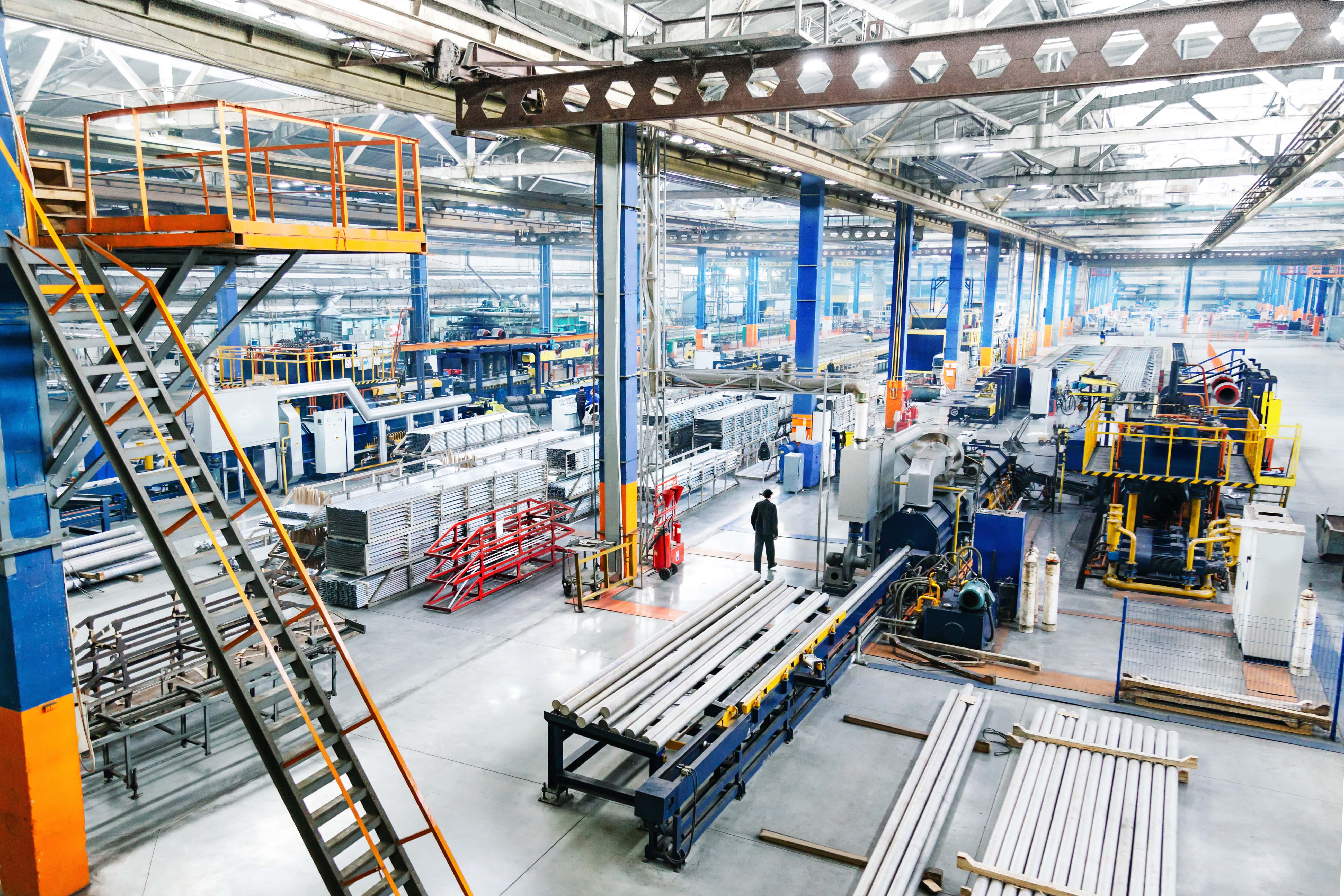
Why Temporary Staffing Fails in Manufacturing & What to Do Instead
Moving from temporary quick fixes to sustainable staffing solutions means making a smart investment in your operation's future. It does require upfront commitment, but the payoff is immediate and transformative: dramatically lower turnover rates, consistently higher productivity, and freedom from the administrative chaos of constant hiring.
For manufacturing and HR leaders, the temporary staffing model that promised quick solutions has become the biggest operational headache. While temp agencies offer immediate workforce placement, they can create more problems than they solve for production environments that demand consistency, reliability, and measurable results.
The manufacturing sector's labor shortage isn't just about finding people to fill positions. According to a Deloitte and Manufacturing Institute survey, the manufacturing industry will face a shortfall of 2.4 million workers by 2028. You need skilled, committed workers who understand the gravity of production deadlines, safety protocols, and quality standards. Traditional temporary manufacturing staffing often fails to deliver these requirements, leaving plant managers and operations leaders searching for effective staffing solutions that actually work.
The Real Cost of Manufacturing Staffing Problems
Temporary manufacturing staffing agencies promise speed and flexibility, but manufacturing environments expose the tough reality of this approach. High turnover rates create significant challenges for temp placements, with the temporary and contract staffing industry experiencing a 419% annual turnover rate. Workers treat assignments as short-term income rather than career opportunities, creating operational chaos that spreads throughout your entire production floor.
Training costs can get out of control when workers cycle through positions every few weeks or months. Small companies spend an average of $1,100 per employee on training costs, while larger companies lose approximately $500 per employee. Every new placement demands safety orientation, equipment training, and process familiarization. Company supervisors and experienced workers get pulled away from productive work to manage constant onboarding, multiplying the true cost of temporary staffing.
Quality control collapses when temporary workers lack long-term investment in outcomes. Without commitment to your company's success, temp workers prioritize speed over precision, driving up defect rates and forcing costly rework. These quality failures ripple through your entire production chain, damaging customer satisfaction and threatening your brand reputation.
Attendance becomes a daily gamble with temporary placements. Workers juggling multiple temp assignments or treating positions as stopgaps deliver inconsistent attendance patterns. This unreliability forces you to maintain larger crews than necessary, inflating labor costs while destroying productivity gains.
Short Term Manufacturing Staffing, Long Term Headaches
The temporary manufacturing staffing cycle creates operational instability that manufacturing leaders can’t afford. Consistent workforce availability drives production schedules, yet temp workers create a revolving door that makes reliable planning impossible.
Safety risks also increase with frequent personnel changes. Manufacturing environments require strict adherence to safety protocols, and temporary workers often lack the deep familiarity with equipment and procedures that prevents accidents. Each new placement represents a potential safety liability until they develop site-specific knowledge and habits.
Beyond safety concerns, team dynamics suffer under constant flux. Experienced workers become reluctant to invest time in training temporary colleagues who may disappear without notice. This reluctance creates knowledge silos and prevents the collaborative culture essential for efficient manufacturing operations.
Administrative burden grows exponentially with high turnover. HR departments spend disproportionate time managing paperwork, conducting orientations, and coordinating with manufacturing staffing agencies instead of focusing on strategic workforce development. This administrative overhead diverts resources from initiatives that could improve overall operational efficiency.
What Manufacturing Leaders Need
Manufacturing success demands three critical workforce elements: consistency, commitment, and control. Traditional temporary staffing delivers none of these requirements, leaving your operations vulnerable to disruption and inefficiency.
Consistency means predictable daily attendance and performance standards you can count on. Manufacturing schedules operate on thin margins, and workforce reliability directly determines your production capacity. Management needs absolute confidence that your teams will show up ready to work, day after day, without the stress of wondering who might not appear.
Commitment means workers who see their positions as career opportunities, not temporary paychecks. Committed employees invest in learning the processes, improving efficiency, and contributing to problem-solving efforts. This long-term perspective drives the continuous improvement that manufacturing environments require to stay competitive.
Control means the ability to plan workforce needs, manage performance standards, and address issues directly. When manufacturing staffing agencies serve as intermediaries, you lose direct influence over worker selection, training, and accountability. This separation creates communication gaps and reduces your management effectiveness.
From Quick Fixes to Sustainable Staffing Solutions
Smart manufacturing leaders are abandoning temporary manufacturing staffing for comprehensive workforce partnerships that solve root causes rather than symptoms. Good Labor Jobs has spent over 20 years perfecting this approach, creating stability that transforms production growth through long-term relationships rather than short-term band-aids.
Successful staffing solutions focus on worker retention through comprehensive support systems that serve your needs first. Rather than treating labor as a commodity, this approach recognizes that satisfied, supported workers become productive, loyal team members. This perspective transforms workforce management from a cost center into your competitive advantage.
Housing and transportation services eliminate the barriers that kill consistent attendance. When workers have reliable housing and guaranteed daily transportation, they focus entirely on job performance rather than daily logistics. This full-circle support creates conditions for success that temporary manufacturing staffing simply cannot match.
Pre-screening and skills verification ensure that placements meet your specific manufacturing requirements from day one. Instead of hoping temporary workers possess necessary capabilities, established staffing solutions like Good Labor Jobs verify qualifications and cultural fit before placement through their proprietary recruiting pipeline developed over two decades of serving manufacturers like you.
Long-term commitment agreements align worker and company interests. When workers commit to extended assignments, they develop deeper understanding of processes and stronger relationships with permanent team members. This investment creates the stability that manufacturing operations require for optimal performance.
Performance monitoring and ongoing support maintain high standards throughout the employment relationship. Rather than placing workers and moving on, full-service staffing solutions provide continued oversight and problem-solving assistance. This ongoing involvement ensures that initial placements develop into long-term successes, delivering guaranteed results through sustained engagement.
Building Staffing Solutions That Transform Operations
Manufacturing leaders who embrace full-service staffing solutions see dramatic improvements in key performance indicators. Recent research reveals that 78% of US manufacturers report voluntary turnover rates of 10.1% or higher for hourly workers, proving how widespread retention challenges have become. Quality metrics improve as committed workers take ownership of outcomes rather than treating positions as temporary assignments.
Training costs plummet when workers remain in positions long enough to justify your investment. According to research from NAM and The Manufacturing Institute, manufacturing organizations invest an average of 51.4 hours per employee in training and are increasing overall investment in training by an average of 60% in response to the growing skilled labor crisis. Instead of repeatedly training temporary replacements, your manufacturing teams can focus on skills development and process optimization with stable workforce foundations.
The Path Forward
Manufacturing and HR leaders ready to eliminate temporary staffing headaches need partners who provide full-circle support, not simple placement services. The most effective staffing solutions combine thorough screenings, long-term commitment, and ongoing support to create sustainable competitive advantages.
Long-term success demands workforce reliability that temporary staffing simply cannot deliver. By partnering with Good Labor Jobs, you get the stable, productive teams that drive sustained growth and competitive advantage through comprehensive worker support.
Ready to transform your manufacturing workforce strategy? Contact Good Labor Jobs today to discover how full-service staffing solutions can eliminate the costs and complications of temporary labor while building the reliable, committed teams your operations need.